We are qualified for the following fusion procedures:
Butt Fusion is the process of two pipe-ends brought into contact with a heating element. After the removal of the element, the molten pipe-ends are pressed together – creating a monolithic entity. Heat fusion joining is a leak proof process and the most common joining method of HDPE. The internal bead of butt-fused HDPE piping systems does not influence the flow rate and pressure of the pipe system.
Electro-Fusion is another HDPE jointing method, where two pipe-ends are fitted and melted into an electro-socket. A heating coil integrated into the electro-socket melts the material surrounding the coils and becomes part of the pipes inserted into the ends of the socket. After cooling, a leak proof joint forms. Flange joints are also suitable for the transition to other pipe materials and for the integration of accessories into the piping system. We use Central Plastics and Friatec Electrofusion couplings and processors.
SOCKET FUSION IS A FAST AND EASY WAY TO ASSEMBLE PIPING SYSTEMS. Polyethylene socket fittings fuse over the pipe wall, making the joints the strongest part of the entire system. Socket fusion uses hand-held welding irons and is used for pipe and fittings ½” to 4″ in diameter. A proper socket fusion involves cutting the pipe, marking it for insertion depth, heating the pipe and fitting for a specified time, and then pushing them together to cool. The fittings are specially sized to create enough pressure with the pipe for a proper fusion. Once cool, the pipe and socket fitting become a single piece with no potential leak path.
Saddle Fusion is used to join service saddles, tapping tees and branch saddles to a Polyethylene pipe main. Sidewall fusion is, like butt fusion and socket fusion, another process based on hot plate welding. Sidewall fusion differs from either socket, or butt fusion methods by performing fusion into the side of the pipe wall in a transverse orientation to the main pipe, rather than in line with the pipe. Sidewall fusion is typically employed in conjunction with either socket or butt fusion methods as a complementary process and many fusion machines designed for butt fusion are also equipped for sidewall fusion. Adaptor plates that match the outside diameter of the main pipe are applied to the heating plate to perform this type of fusion.
Exterior Manifold
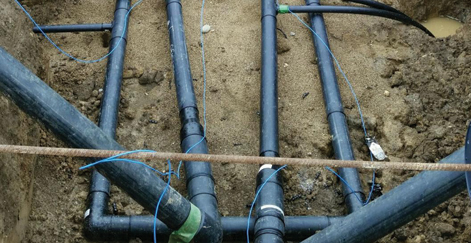
Trench layout, dig or excavate trench to appropriate depth, apply bedding materials such as sand for pipe protection against sharp or large objects like rocks.
If large rocks come from the excavated trench they will not be put back in trench and also some locations or contractors require trace wire.
Fusion Header Building
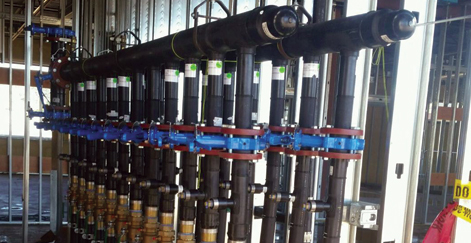
Building interior, loop fusion into header supply and return lines.
Flushing / Cleaning
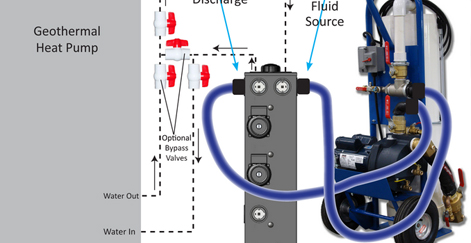
This is one of the most important procedures that needs to be followed in order for the system to function properly.
Flushing: removal of all debris such as dirt, sand, pipe shavings, teflon tape and other items that can get in the pipe during the fusion process.
Purge: removal of air trapped in the lines vertical and horizontal since the loops can go as much as 300ft down into earth and the water needs to be moved at a certain speed to push the air out of the pipes.
Saddle Mounting
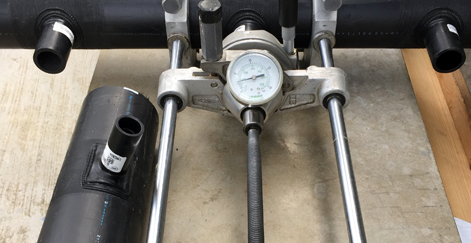
This is a fusion procedure and it would vary from 1-1/4 pipe up to 8″ pipe that is on the main pipe and the branch would go from 3/4″ up to 4″
1″-1/4 – 3/4 | 1-1/4-1″ | 1-1/2-3/4″ | 1-1/2-1″| 1-1/2-1-1/4 | 1-1/2-1-1/2 | 2″-3/4″ | 2″-1″ | 2″-1-1/4″ | 2″-1-1/2″ | 2″-2″ | 3″-3/4″ | 3″-1″ | 3″-1-1/4″ | 3″-1-1/2″ | 3″-2″ 3″-3″ | 4″-3/4″ | 4″-1″ | 4-1-1/4 | 4″-1-1/2″ | 4″-2″ | 4″-3″ | 6″-3/4″ | 6″-1″ | 6″-1-1/4″ | 6″-1-1/2″ | 6″-2″ | 6″-3″ | 6″-4″ | 8″-3/4″ | 8″-1″ | 8″-1-1/4 | 8″-2″ | 8″-3″ | 8″-4 | 8″-6″
Pump Installation
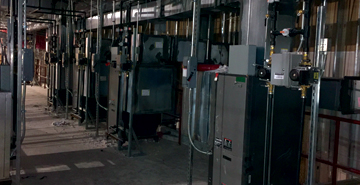
Most water source heat pumps come with a built in pump and some do not and they are to be mounted in a close proximity of the unit.
Circulating pumps eventually have to be changed either because they will just go bad or with the years of service they would start getting clogged up because of minerals in the water . In the event to replace the circulating pump the system would have to get flushed and purged to have the system back performing properly.
Purge Valve Replacement
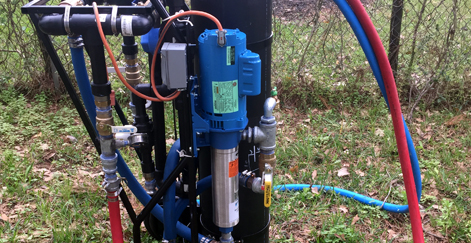
Purge ports and purge valves replacement: a few years ago geo contractors used brass ball valves on exterior purge box and they would only last a few years then they had to be replaced. There are many systems in place with these type of valves and pipe manufacturers make a valve made of the same material (polyethylene) and it can be buried or be installed in a purge box and it will last forever.